Prof. Kenichi Ohno, National Graduate Institute for Policy Study (GRIPS)
My first encounter with Dr. Nguyen Dang Minh was at the Vietnamese-Japanese Students Conference held in Kyoto in November 2008. He was presenting his own theory of production line improvement. Dr. Minh learned automotive repair and maintenance in Japan, then studied at Tokyo University for a master’s degree and at Nagoya University for PhD. He also worked at the Production Engineering Department of Toyota Headquarters for seven years. Upon returning to Vietnam, he taught at a university and set up his company, including GKM Lean Institute in 2015. Despite his brilliant career so far, he has a very friendly and informal personality.
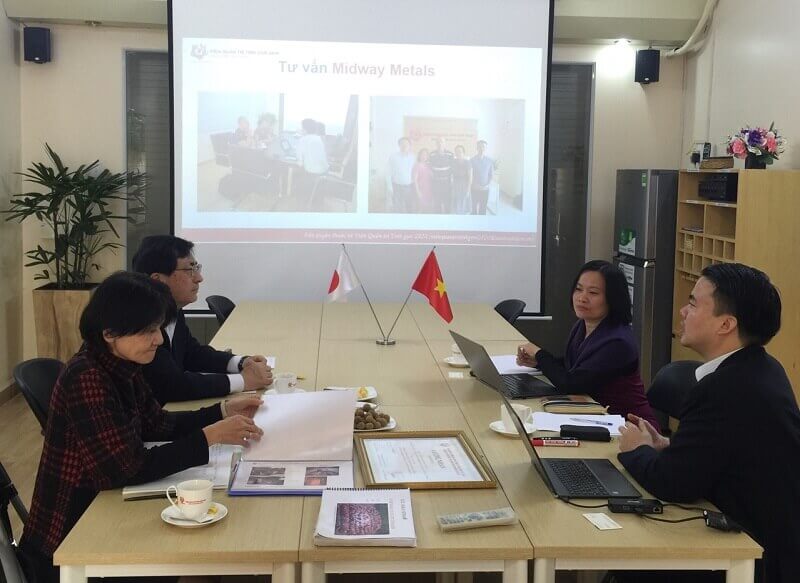
Prof. Kenichi Ohno and Prof. Izumi Ohno visit GKM Lean Institute
Dr. Minh believes that monozukuri (manufacturing) must start with the right “TAM THE” (somehow, mindset) without which no technical learning or introduction of kaizen tools will be sustainable. This principle applies not only to manufacturers but services, families and governments as well. The TAM THE proper to the Vietnamese people must be developed by the Vietnamese people, and this is what he has been doing by combining both theory and practice. His Institute is supported by his wife, brother and former students to spread Dr. Minh’s belief and method. I am also closely following Dr. Minh and his company because they are key industrial experts with deep knowledge of Japanese language, culture and manufacturing. To transform Vietnamese society, government’s policy and Japanese cooperation are important, but the most critical thing is sincere effort and action by the Vietnamese people themselves. Japanese Ambassador Kunio Umeda highly appreciates Dr. Minh’s endeavor and has invited him to speak at many industry-related events and activities.
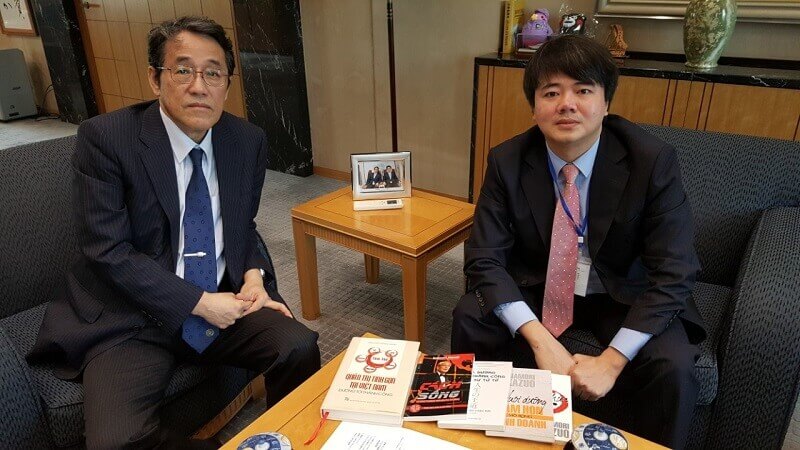
Prof. Nguyen Dang Minh discussed with Ambassador Umeda on the topic of TAM THE and Made in Vietnam Lean Management
GKM Lean Institute has already transformed many Vietnamese people and companies. Among them, I have personally visited and/or received detailed reports from Dr. Minh on a number of companies, including Truong Hai (major automotive assembler), Hai Phong (dispatcher of Vietnamese technical interns to Japan with high-quality training and support), Le Group (suppliers of pressed and welded components to Japanese motorcycle assemblers), and Julie Sandlau (exporter of jewelry products to Europe, America and Japan). What is very important about these companies is that the radical transformation of TAM THE and efficiency is clearly visible. The director general and employees are also aware of their own progress, thank Dr. Minh for it and are very happy. They are not saying nice things superficially or diplomatically. The fact that such a company-wide revolution is possible in Vietnam, and that it is guided by a new method developed by Dr. Minh who knows both Japan and Vietnam very well, is truly amazing and deserves attention.
Dr. Minh’s book, Lean Management in Vietnam: The Way to Success (in Vietnamese), does not explain his method very clearly, and this is natural because it is a trade secret. From my experience of visiting companies and talking to Dr. Minh, his method includes total delegation of authority from the DG, intensive discussion with all department heads, and the drafting of standard manuals for all workplaces, among others. Such heavy and deep guidance cannot be done by Japanese experts who must speak through an interpreter.
Dr. Minh’s grand design goes far beyond corporate consultation. He also targets CEO management seminars and training program, Made in Vietnam 5S at families through courses and actual visits, instruction in technology, establishment of a private school, production of devices and materials for teaching monozukuri (manufacturing), and TAM THE tutoring service for children by trained students. Some of these have already started. In the future, he also wants to create a Vietnam-Japan business and cultural center. The concept is similar to the Vietnam-Japan Institute for Human Resources Development supported by JICA, but his will be highly action-oriented and privately operated. His plans have no limits, but he and his company are unlikely to have sufficient time or finance to realize all these. It will be vital to expand the network of followers and supporters, increase competent Vietnamese instructors, and receive assistance from Japanese firms and government where needed.
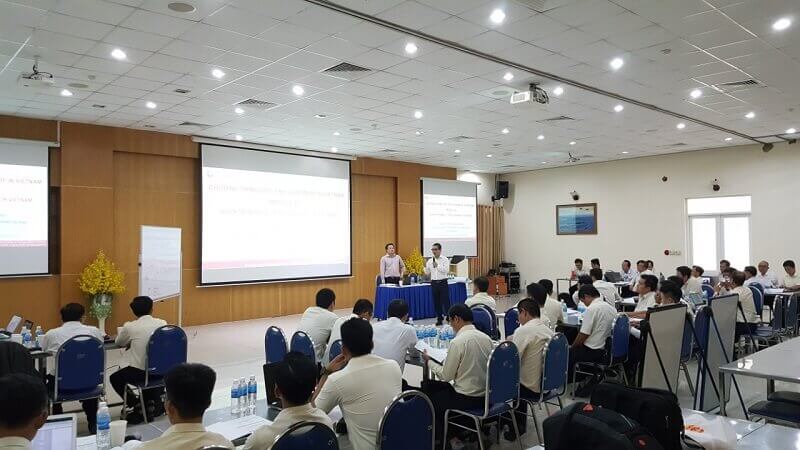
CEO Training Program of GKM Lean Instittute
Dr. Minh may think that his method is unique to Vietnam. I feel that it contains both globally common elements and locally unique ones. All teaching methods have these two elements. My research interest is comparison of industrial policy in Asia and Africa and conducting policy dialogue with any wiling government. In the last eleven years, I had very intensive discussions with Ethiopian prime ministers and economic ministers. Ethiopian managers and workers also lack proper mindset. In South Africa, automotive assembly plants complain about the slack discipline and slow learning of local employees. Sri Lanka, now an exporter of high-end apparels to western markets, initially suffered from unproductive workers. In Cambodia, some Japanese firms mobilize a Buddhist monk to teach proper TAM THE (mindset) to workers. The truth is that the mindset problem is widespread in many countries. I believe these countries can learn a lot from the method developed by Dr. Minh. However, they should not simply copy-and-paste this method but should modify it to suit their domestic situations. In the near future, I would like to ask Dr. Minh to visit Africa and have discussions with business leaders and policymakers there.
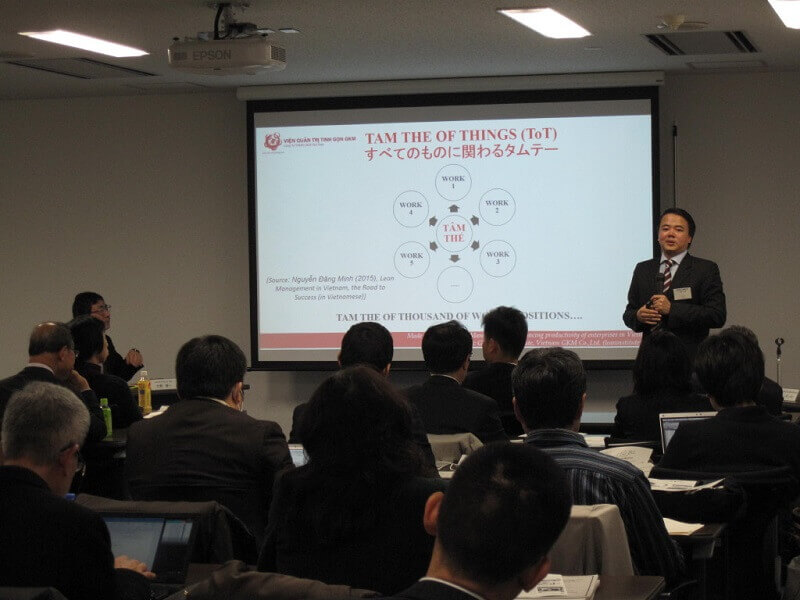
Seminar of TAM THE and Made in Vietnam Lean Management at GRIPS